在纺纱过程中,棉结数量直接影响半成品的内在结构,也影响牵伸过程中纤维的运动。棉结会带动周围的纤维成束或成团地变速,致使条干恶化,还会和周围纤维聚集而形成粗节,直接影响成纱外观。因此,在对原料及纺纱各工序棉结数量进行分析的基础上,找出影响成纱结杂的主要原因,以便采取有效措施控制成纱结杂,提高纱线质量。
1成纱结杂成因分析
1.1结杂成因分析
杂质是因棉花采摘、摊晒和加工过程中掺人一些非纤维物质以及不孕籽、破籽、棉籽等造成的,多数杂质在生产过程中能够除去。棉结成因比较复杂,一类是原棉初加工造成的,原棉根据轧工方式分为皮辊棉和锯齿棉两种,锯齿棉与皮辊棉相比,锯齿棉带纤维籽屑、棉结等疵点多,但含杂率相应比较小,带纤维籽屑和棉结在纺纱过程中不易被排除。另一类是在生产过程形成的棉结,纤维在加工过程中经过打击分梳和牵伸易扭结在一起形成白星,一旦形成棉结,在后工序中就无法除去。
1.2纺纱过程中棉结杂质的分布规律
棉结、杂质在各工序中有一定的分布规律,图1为CJ 11.81 tex品种在纺纱各工序中棉结、杂质分布的大致情况。
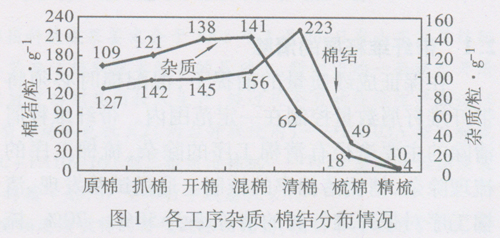
由图1可知,在纺纱过程中开清和梳棉工序是产生棉结和清除棉结的关键工序,而开清和梳棉又是除杂的重要工序。因此,要减少成纱结杂粒数,必须先控制清梳两工序的结杂粒数。
1.3原棉物理性能的影响
采用三种配棉进行纺纱试验,验证原棉性质对成纱结杂的影响,三种配棉方案见表1。

配棉一为成熟度、整齐度好,棉结、杂质、短绒少,带纤维籽屑少的长绒棉;配棉二为成熟度、整齐度一般,棉结、杂质、短绒较少,带纤维籽屑较少的长绒棉;配棉三为成熟度、整齐度差,棉结、杂质、短绒较多,带纤维籽屑较少的长绒棉。不同配棉在相同工艺条件下纺CJ 11.81 tex纱,成纱质量对比见表2。

表2试验数据表明,在三种配棉状况下,随着原棉质量的下降,梳棉、精梳工序半制品的棉结、杂质增加,细纱各项物理指标恶化,这是由于原棉的成熟度、整齐度、棉结、杂质、带纤维籽屑所引起的。成熟度差的原棉,纤维刚性低,容易扭曲且缺乏恢复的能力,在纺纱过程中易形成棉结。棉籽表皮的棉籽附着力小,轧棉时容易造成带纤维杂质,而这种杂质在纺纱过程中易分裂,从而增加了成纱杂质粒数。纤维中的短绒在开清棉和梳棉过程中易形成棉结,在细纱中会产生粗节、细节,而短纤维含量与整齐度关系密切,一般短绒高,整齐度就较差。
2减少成纱结杂的措施
2.1带纤维籽屑的清除
在保证成纱质量的前提下,混配棉时必须将带纤维籽屑数量控制在一定范围内。带纤维籽屑清除的主要途径有清棉工序的除杂,梳棉工序的梳理除杂,精梳落棉率的控制。通过试验发现,清棉工序对带纤维籽屑的清除率为50%~70%,梳棉工序为70%~90%,精梳工序为80%~90%,因此,提高梳棉和精梳工序的清除效率是减少带纤维籽屑数量的关键。
2.2 改进开清棉工艺,提高棉卷质量
清棉工序既是主要的除杂工序,又是棉结增加的主要工序,在工艺方面采取多松少打、轻打早落、少碎少返的原则,主要调整以下几个方面:(1)在往复抓棉机上减少抓棉机的抓取量,抓棉机下降距离由原来的4 mm改为3 mm,刀片伸出筋条距离由5 mm改为3 mm,提高抓棉机运转效率达85%以上,做到少抓、勤抓,提高开松度;(2)充分发挥棉箱的均匀混和作用,均棉罗拉的隔距在保证供给的前提下尽量缩小,减小压棉帘与角钉帘隔距,使棉箱运转率达到85%以上;(3)各机尘棒为减少挂花,全部进行电镀.隔距也放到最大,使杂质早落多落,将A10型抓棉机打手、B10型开棉机打手改造成稀密式锯齿刀片,增强分梳能力。
2.3控制好生条中结杂数
生条中的棉结、杂质直接影响到梳棉以后各工序纺纱牵伸时纤维的运行状态,因此,采取以下四项措施提高生条质量:(1)锡林与刺辊的线速比由1.73增加到2.03,有利于棉纤维从剌辊向锡林转移;(2)增加盖板速度,由162 mm/min增加到196 mm/min,加强细小杂质与短绒的清除;(3)减小小漏底入口隔距由8 mm改为6 mm,增加后区落棉;(4)增加固定分梳板,锡林盖板隔距由0.23 mm、0.20 mm、0.18 mm、0.18 mm、0.20mm改为0.18 mm、0.15 mm、0.13 mm、0.13 mm、0.15 mm,加强对棉纤维的分梳。
清梳工艺调整前后棉结、短绒测试见表3。
表3数据表明,通过对清梳工艺的调整,提高了纤维的开松度,使杂质早落、多落、少碎,加强分梳,多排纤维短绒,使清棉、梳棉输出半制品结杂数控制在较低的范围内。
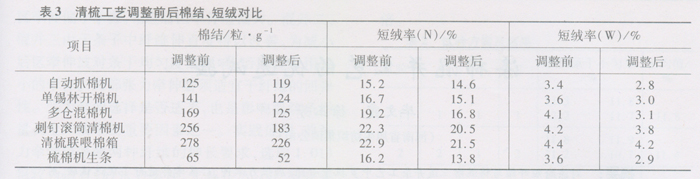
2.4合理控制车间温湿度
原棉含水率高,纤维间抱合力大,刚性低,易扭曲,杂质不易清除,成纱棉结、杂质增加;原棉含水过低,杂质容易破碎,造成棉结增加。梳棉棉层回潮较低时,杂质容易下降,棉结也可减少,一般应控制棉卷回潮率不超过8%。清棉车间相对湿度一般控制在55%~60%,温度控制在25 ℃~30℃,使棉卷放湿,增加纤维的弹性,减小纤维与针布摩擦。
3 结束语
(1)应掌握原料的特性,尤其是原棉的成熟度、整齐度、短绒率、棉结、杂质特性,根据纺纱质量要求,合理配比,保证成纱质量。
(2)带纤维籽屑在纺纱过程中的清除主要靠梳棉和精梳工序,尤其以精梳清除率最高。
(3)锡林与盖板之问紧隔距工艺能有效地增强分梳强度,减少生条中的棉结数。
(4)在一定范围内增加锡林与刺辊的线速比,利于纤维向锡林的转移,提高纤维的梳理效果,同时提高盖板速度,清除短绒和小杂,降低生条含杂量。
(5)清棉工序的关键在于杂质的早落、多落、少碎,开清棉输出品的结杂数是一个重要指标。
(6)根据原料性质合理控制清棉车间温湿度,尽量减少在纺纱过程中纤维的缠结、损伤。