关键词:工艺、纤维损伤、连续均匀喂给、薄喂柔和开松、梳理转移适度、结杂短绒兼顾、工艺参数保证、梳理元件、变频器、工艺速度、工艺隔距、棉结、短绒
概述
由于清梳联工艺技术的不断完善和提高,在国内外纺纱工艺的生产及设备中所占的比重日趋增大.而且清梳联工艺适纺的工艺领域不断拓宽.在环锭纺工艺生产中,从普梳到精梳,从中支纱到高支纱(Ne60-80支);在转杯纺中,从低支纱到中支纱(Ne7-32支);适纺原料从纯棉到化纤,及各种异性纤维等,清梳联适应的工艺领域不断地拓宽.
由于清梳联生产线用人工可减少60%以上;制成率可在百分之90%以上等经济方面的突出效益.使清梳联工艺从技术经济效果上考虑,取代传统纺纱成卷工艺的比重越来越大.因此,深入研究清梳联工艺质量与成纱质量的相关性,进一步实现纺纱工序自动化、连续化和高效、优质的水平,已成为世界纺织同行共同关注的问题.
本人认为 在研究、开发清梳联工艺过程中,主要影响成纱相关质量指标的是纺纱工序中作为半成品的生条的棉结、短绒、杂质的成因和棉条均匀度的变化规律.这是深入研究、开发清梳联的主要工艺技术内容.
借助科学地检测手段(如:AFIS、HVI等仪器)分析在纤维加工过程中,棉结、短绒和杂质变化情况,使人们可以剖析从原料到筵棉再到棉条(包括生条、熟条和粗纱条)的全过程工艺质量的变化
对此,可以对清梳联每道工序的工艺参数、结构调整和改进中进行优化,以取得更优的纤维加工效果.最终实现以下目标:
⑴.最大限度地减少纤维损伤-即减少12.7到16毫米短绒率的增加;
⑵.最大限度地减少清花工序中棉结的增长率;提高梳棉工序中棉结的去除率;
⑶.最大限度地去除原棉中的杂质-即提高清梳工艺过程的除杂效率,以减少生条中的含杂率;
⑷.提高生条的不同片段的均匀度.
以下结合青岛清梳联的生产工艺流程的生产质量控制,分别进行叙述如何实现上述质量目标。
一、清梳联工艺流程及特点
清梳联工艺流程以一台抓包机供应6-10个梳棉、喂棉箱、调匀整单元组装置组成一条生产线即“一机一线”为例:
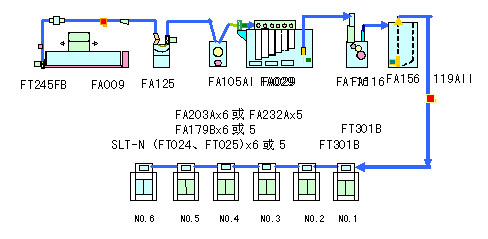
图中:
FA009自动往复抓棉机 FA125重物分离器 FA105AI单轴流开棉机、FA029多仓混棉机、
FA116主除杂机 FA156除微尘机 FA179B喂棉箱FA203A或FA232A梳棉机、
SLT-N、FT024、FT025自调匀整器 FT301B连续喂棉装置
现清梳联工艺流程中,抓取、开棉、混棉和清棉的工艺要求都由提高单机工艺效率来完成,避免了传统的多点重复打击造成对纤维的损伤和增加棉结,在确保实现产量和棉结、杂质、短绒工艺质量的目标下尽量简捷流程。
二、 清花工序与工艺质量
清花工序主要根据不同的原料和纺纱品种,确定打手形式、工艺速度和隔距:在清花工序应尽量减少对纤维的损伤和棉结的增加;一条好的清花生产线,该工序的短绒增加率一般不应超过1%;棉结增加率一般不应超过75%(注);根据原棉的含杂率确定除杂效率.实现清花、梳棉合理的分担.清花除杂效率由30%至65%不等(与原棉含杂率成正比)。清花工序的工艺质量靠以下措施保证:
1、实现“薄喂柔和开松”,减少纤维损伤。
清棉工序采取短流程的开清工艺以减少对纤维的重复打击,是减少纤维损伤的关键;而精细抓棉和高效除杂是开清机组实现短流程的基础。在整个清花工艺流程中,通过采用交流变频器,可以根据原料和产量的需要,方便而精细地调整给棉罗拉,打手和风机的工艺转速,以获得最佳的工艺状态,即在尽力减少纤维损伤的同时,实现对棉束进行开松和除杂。
1.1、抓棉机工艺参数的优化
对于自动往复抓棉机而言,我们可以通过调整小车往复速度、抓取辊速度、抓取辊刀片伸出肋条隔距和抓棉臂每次下降动程等参数来实现精细抓棉。
在通常情况下,抓取辊速度和抓取辊刀片伸出肋条隔距调整好后是不再变动的,保证质量主要靠变动抓臂往复速度和抓臂下降动程来实现(可在控制箱面板上设定)。
但在实际的生产中棉包密度差异大,进口棉包密度要比国内棉包大的多;“捡三丝”后各厂打包的密度也不一样,有的甚至不打包.在此情况下,如何保证自动抓棉机实现精细抓棉就要区别对待。
例如:有的厂家棉包过松,为保证供棉,小车往复速度高达18米/分;抓臂每次下降的动程也相应较大.为此,抓取棉块较大,为保证除杂和均匀混棉的效果,不得不增加开棉和混棉的设备,造成对棉束的重复打击,这必然会增加纤维损伤。通过使抓取辊采用变频调速,以适应不同的棉包型式,这为根据不同原料、纤维成熟度、细度的不同等优选抓取辊速度(一般设置在1000-1350转/分之间)、实现精细抓棉提供了方便。
另外,现在已有比较成熟的异性纤维拣除装置.采用该装置后,可以不用人工捡三丝,从而保证了抓棉机抓取紧包而不是松包,为精细抓棉提供条件。
1.2、主要开松设备应配有变频器,可实现各机喂棉罗拉和打手速度的优化,适应不同原料和产量.
以青岛清梳联设备为例,FA105A单轴流开棉机和FA116主除杂机,不同的打手速度对棉结、短绒的变化率有明显的区别。一家在国内有影响力的用户用AFIS曾做了FA105A单轴流开棉机、FA116主除杂机不同打手速度试验,分别见表1、表2:
(试验条件:原棉性能--品质长度:27.33毫米,马克隆细度值:4.24,强度:28.12,含杂率:1.5%,棉结:312粒/克,16毫米短绒率:15.2%,FA105A产量:660公斤/小时,FA116产量:330公斤/小时)
表1 FA105A打手速度与棉结,短绒(AFIS)测定值
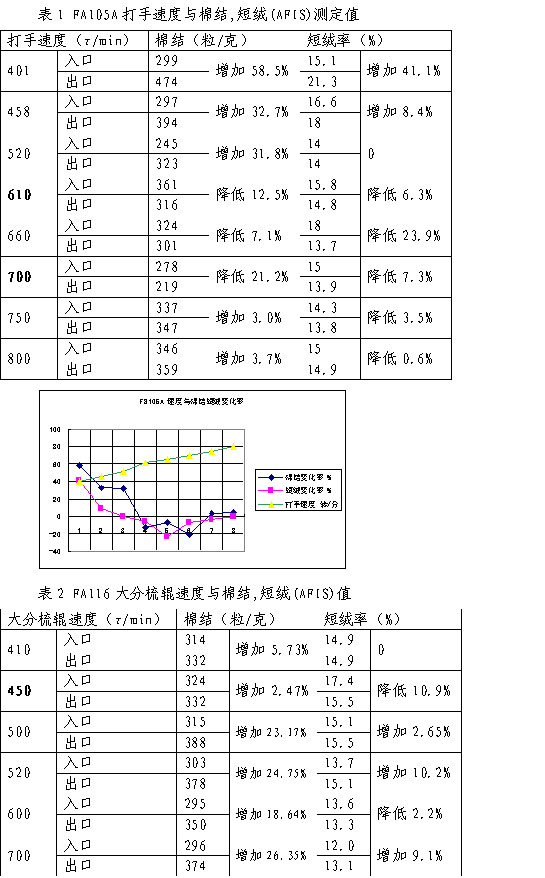
从表1、表2的数据可以看出,相同的产量,不同的打手(或分梳辊)转速,棉结和短绒的变化率并不相同。
同时,我们曾就同一机台进行过不同产量、相同转速的工艺试验,试验结果表明:不同的产量时,对打手应采用不同的转速--产量高时,转速应适当提高;产量低时,转速应适当降低。
从大量同产量不同打手速度、同打手速度不同产量的试验可以得到如下结论:打手速度不应采取恒定速度,而应根据不同的产量,不同的原料确定不同的速度,这样可以在保证单机工艺任务的前提下,尽可能减少纤维损伤。
以上试验结论为:清花设备打手采用变频调速,以方便根据不同产量调速提供了依据。
1.3、清花工艺流程中的气流参数要保证.各输棉风机都采用变频调速,实现了在合理地气流参数下输送棉束并获得最佳气棉比。
2、合理配置开松元件,实现薄喂柔和开松,减少纤维损伤
2.1、采用V型角钉代替其他型式打手
FA105A单轴流开棉机采用V型角钉,该种角钉富有弹性,开松柔和、充分;同时由于FA105A的结构可以使棉流随打手旋转5周半,实现棉束在打手与尘棒间棉杂分离,反复除杂;且该清棉过程为棉束呈浮游状态下进行自由打击,其纤维长度、弹性和强力可基本保持不变.不会因握持打击而增加棉结和短绒。所以,只需处理好进棉口、出棉口、出杂口、排风口的气流参数(静压与风量),调整好四个区的尘棒隔距,采用适当的打手速度,即可达到最优的工艺效果。
2.2、选用针辊代替锯齿辊筒减少纤维损伤
使用实践证明:为了进一步减少纤维损伤,降低短绒率,在降低主除杂辊转速的同时,选用针辊代替锯齿辊筒。以FA116主除杂机为例,当大分梳辊采用针辊后,短绒率较锯齿型可减少1%左右。
为何针辊有如此好的效果?本人认为:针辊和锯齿的主要区别在于其针齿形状.针辊的针是圆形的,针尖锐利但很光滑,可以很好地穿刺于纤维之间达到开松纤维的能力,由于纤维自由地浮于针尖因而并不被损伤;而锯条针齿的横截面是矩形的,当其握持的纤维在针齿表面移动时,锋利的矩形断面会对纤维造成一定的切割损伤。
3、流程采用连续均匀喂棉,实现棉流密度一致和梳理负荷均匀。
采用“全流程连续均匀喂棉”的控制技术,为实现生条不同片段的重量一致性提供了良好基础。所谓“全流程连续均匀喂棉”,就是在全流程喂给系统采用压力传感器调控和变频调速装置,使单机运转率达到100%,做到连续输送棉流。这样在保证生产供给的前提下,可以最大限度的做到棉束小、棉流均匀,为各机细化工艺参数,提高各项工艺质量指标打下基础。
从该清梳联配置来看,提高FA029多仓混棉机的运转率是保证整个流程中各机台高运转率的核心。为达到这一目的,FA029多仓混棉机的斜帘、水平帘子均采用变频调速。斜帘的运转率受其下游机台FA116主除杂机上棉箱内部压力传感器和喂棉罗拉的控制,经调试后可以达到100%;水平帘子受控于斜帘子的速度,只要设定好棉仓压力范围即可。这样就为提高FA009自动往复抓棉机运转率创造的条件,FA009的运转率一般都在90%以上,在一定的质量下,根据原料情况采用小单元排包工艺,不仅做到抓取棉束最小,而且也可以做到抓取每一个单元的原料次数相同,同时增加抓臂长度来增加排包数量实现对原料的混合也可以起到很好的效果。
三、 梳棉工序与工艺质量
梳棉机工序主要完成分梳、除杂和成条工作,生条的结、杂、短绒和不匀率等直接影响最终的成纱质量。若不经过精梳,梳棉机是纺纱工艺中最终的去除棉结、杂质和排除短绒的唯一工序;虽然有的工艺中末道并条机装有自调匀整器,但梳棉生条的重量不匀率仍很重要。
我们通过减少FA179B喂棉箱的棉结增加量、选用优质的梳理元件、优化的工艺速度和精确的工艺隔距做到梳棉机棉结、短绒兼顾、控制生条重量不匀率等措施来保证梳棉工序的纤维工艺质量。
1、 减少喂棉箱的棉结增加量
上棉箱给棉罗拉采用变频调速能使其根据下棉箱压力变化改变转速,同时其运转速度应根据产量需要设定,从而做到薄喂柔和开松,减少纤维损伤;原料喂给采用顺向喂棉,也可减少纤维损伤;开松辊的转速对棉结影响较大,一般规律是:速度越高,棉结增加量越大;速度越低,棉结增加量越小,所以要在保证必要的开松的前提下,尽量降低开松辊的转速。在采用原设计速度的60%对比时,取得较好的工艺质量效果;同时开松辊应采用梳针型,钢针针尖呈圆弧形,既能穿透纤维又能减少纤维的损伤。
2、 用优质的梳理元件、优化的工艺速度和精确的工艺隔距实现梳棉机棉结、短绒和除杂兼顾。
纤维在梳理过程中,突出的工艺质量问题是棉结和短绒的矛盾.特别是对棉结要求严的最终产品更加显著。梳棉机是去除棉结的主要设备,但它排除短绒的同时,也会产生短绒.在用手工法测试时,生条短绒的增长主要是由梳棉机产生的。为解决这一对矛盾,采取了以下措施:
2.1 优选梳理元件和优化工艺速度。
优选梳理元件主要是指做好梳理元件配套;优化工艺速度是根据产量和针布规格确定不同的工艺速度。因为梳棉机是通过针布对纤维的梳理功能进行有效地控制,实现对每根纤维充分梳理、转移、除杂和均匀混合作用。多年的实践证明,针布的规格与工艺速度对成条质量影响最大。我们曾进行不同规格针布在不同锡林速度的对比试验,发现不同规格的针布在棉结与短绒最优组合点时,工艺速度并不相同,见下图(AFIS测定值):
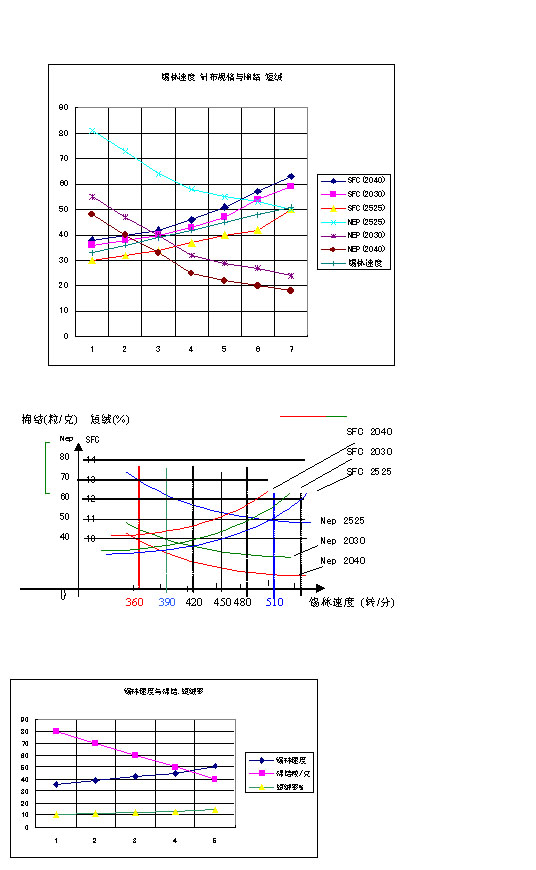
由上图可以看出,随着锡林针布工作角的减小,棉结与短绒达到最优组合点的锡林转速在同时下降,如:2525针布的最佳组合点处锡林速度约为510转/分,2030针布约为390转/分,而2040针布仅约为360转/分
从锡林针布的选型来看,虽然高产梳棉机锡林针布的齿密没有随着产量的提高而同比例提高,但棉条的棉结、杂质水平得到显著提高;成纱质量水平同时得到提高。
本人认为:虽然按传统梳理理论所强调的“梳理度”(锡林上的瞬时纤维支数或密度)(注2)配备新型梳理元件后的高产梳棉机,其锡林上的瞬时纤维支数或密度要大于中、低产梳棉机;蹜(见表3)但就分梳效果而言,高产梳棉机的棉条工艺质量和产量水平均明显得到提高。
表3不同针布规格梳棉机的梳理度(梳棉机产量为40公斤/小时)
梳理度(作用齿数/每根纤维)计算:
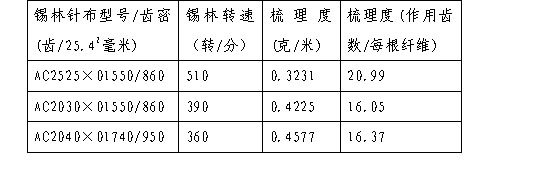
C=Nc.L.Z/1000Wt.Nb(作用齿数/每根纤维)
式中各参数如下:
Nc(锡林转速)
L(纤维平均长度)=29.0毫米
Z(表面总齿数):=π×1288×1000×齿密/25.42齿/转
Wt(喂入量)=666.7克/分
Nb(纤维公制支数)=5700
分析原因:按照传统理论,要保证梳理效果一定要保证梳理度,而实际情况是,当梳棉机产量增大到一定程度时,仅仅靠提高锡林速度而保证所谓传统的梳理度并不能减少生条的棉结数,短绒反而随着锡林速度的提高而逐渐增多,应该说是越来越偏离棉结和短绒的最佳组合点。在这种情况下,仅靠工艺速度已无法从根本上解决问题,应从梳理元件的几何尺寸上重新考虑。因为“梳理度”只是强调锡林表面瞬时纤维量多或少的概念,而实际在梳理过程当中,若针布握持纤维的能力较差时,则可能会出现有些浮游在锡林表面的纤维并没有被盖板和锡林针布所充分梳理,就转移到道夫上,直接影响棉网的清晰度和棉结的数量。为此应选用2030系列针布代替2525系列针布,增加梳理元件对纤维的控制力,保证有效分梳。
同时现在高产梳棉机选用的道夫针布是弧形齿背的,而不再选用直线型齿背的。弧形齿背的道夫针布大大增强了道夫对锡林纤维的凝集能力,减少了锡林上纤维的负荷,使锡林上的纤维不会因为出现多次反复分梳,而造成棉结增加;现在还有的道夫针布侧面设计有多条凸出的棱,这个设计进一步增强了道夫针布握持纤维的能力,该种针布适合于特高产(如纺气流纺)或纺化纤,使高产梳棉机道夫的转移率(注3)进一步提高。
后固定盖板、刺辊分梳板的主要作用是开松纤维,这两种梳理元件控制纤维能力较弱,主要起托持纤维的作用,加大隔距反而减少棉结,目前尚需对针密变化的工艺影响进行探讨。
前固定盖板的主要作用是保持和进一步理顺经过锡林和盖板梳理后的纤维.当此处针布几何形状控制纤维能力较强时,浮游纤维少可减少棉结的产生.所以高产梳棉机现在选用针密提高到每平方英寸的640齿,有的甚至采用针密为每平方英寸860齿的前固定盖板针布。
2.2注重梳棉机隔距的调整
为了提高梳棉机棉条的质量,我们强调梳棉工艺要作到“七快一正”.“快”是指七个分梳点的针尖要锋利;“正”是指隔距要准确一致。
对梳棉机而言,60%-65%的杂质在车肚位置完成,同时明显影响短绒的增减.所以刺辊落杂区大小的调整十分重要。尤其是第一落杂区,该区落棉量占整个车肚落棉的70%,该落棉量需要调整刺辊和给棉板的隔距来实现。
除尘刀与刺辊的隔距、除尘刀的高度和角度对落棉也有很大影响,该隔距不能太小,由于通过刺辊的瞬时棉流密度是通过锡林的瞬时棉流密度的两倍以上,所以该隔距应约是锡林与盖板隔距的两倍。当隔距定好后,可以用除尘刀的高度和角度来调整落棉量,除尘刀角度越小,高度越低,落棉量越大。
刺辊分梳板与刺辊的隔距应根据纺纱品种进行调整,一般为了减少纤维损伤,纺精梳时,该隔距较纺普梳时大,在1.5到2毫米.且要进口大而出口小。
后固定盖板如果隔距过小时,游离纤维反而会被揉搓成棉结.目前,高产梳棉机均采用较大隔距.由进口到出口分别为18″‰,17″‰,16″‰;
刺辊的开松除杂过程会增加棉.,棉结的去除主要靠锡林和盖板之间的分梳区。试验证明,当锡林盖板隔距大于12″‰(英丝)时,棉结会大量增加。这是因为从AFIS单纤维测试仪测的的棉结直径平均在600微米(μm),一般我们将尺寸>400微米(μm)的纤维纠缠体定义为棉结,所以锡林与盖板间的隔距应尽量小,以便将棉结分梳开。
前固定盖板的作用与回转盖板类似,所以该处隔距也偏小掌握,前固定盖板除了减少棉结的作用外,还起理顺和拉直纤维,提高生条中纤维伸直度的作用该处隔距由进口到出口分别为12″‰,11″‰,10″‰。
锡林与道夫之间主要是梳理转移的作用,梳理转移的好,对减少棉结极为有利,所以该处隔距通常在4″‰(英丝)为佳。
3、 生条重量不匀率的控制
生条重量不匀率分为内不匀和外不匀,其中内不匀的大小反映了每一台梳棉机输出棉条的不同片段长度的均匀度,而外不匀则是衡量梳棉机组输出棉条均匀度的重要指标。
3.1改善生条重量内不匀率与偏差值的质量控制方法
影响和改善重量不匀率主要取决于筵棉(或花卷)的喂入(纵向和横向)均匀度;梳棉机的均匀混合作用;连续均匀喂给装置的控制精度;是否采用自调匀整装置及匀整系统形式等因素。
其中,提高筵棉均匀度,通过以下措施来实现:
⑴清梳联系统中,在多工序的棉流转移采用连续给棉控制;保证了清花打手开松均匀;上棉箱各机台存棉稳定;下棉箱输出棉层密度稳定;
⑵采用控制输棉管道及上、下棉箱压力偏差大小,实现输出筵棉重量稳定;
⑶选择控制精度高的压力传感器和交流变频器实现微调控制,使输出棉层连续而均匀;
⑷采用开环或混合环的梳棉机自调匀整装置,即时改变梳棉机欠伸,实现提高棉条长短片段的均匀度;
⑸提高棉花通道及棉条通道光洁度,使棉流输送流畅,减少阻力;有利于提高输出棉条的均匀度。
采用自调匀整与否对输出生条均匀度有着明显影响,可参见下图:
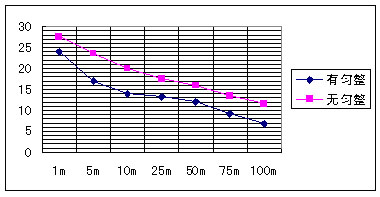
3.2改善生条重量外不匀率与重量偏差值的质量控制方法
在传统清梳工艺中,可以通过控制花卷的重量不匀率和重量偏差来确保生条不匀率和重量偏差;但在清梳联工艺中由于用筵棉代替了花卷,所以必须加强对生条外不匀率和重量偏差的控制才能保证细纱支数的稳定.
影响生条重量外不匀率有以下因素:
⑴梳棉机组各台输出生条重量内不匀率和重量偏差的大小,直接影响机组生条外不匀率的大小.实践证明,梳棉机机组生条重量外不匀率的大小与单机生条重量内不匀率的大小密切相关:
例:某纺织厂清梳联生产线
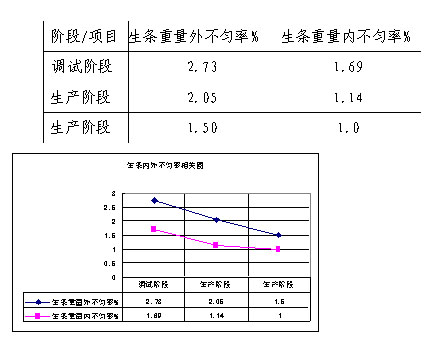
生条重量偏差值的大小反映了生条长度方向的线密度的离散大小,即生条重量实际值偏离设计值的绝对差异,可以用克/5米或设计定量值的百分比来表示;重量偏差值的的大小直接影响生条重量台班内不匀率或台间外不匀率的大小;尽量减小各台梳棉机实际运行重量与设计重量的差异可以明显降低梳棉机生条不匀率;并且影响并条,粗纱和细纱的重量不匀率.见下表(注).
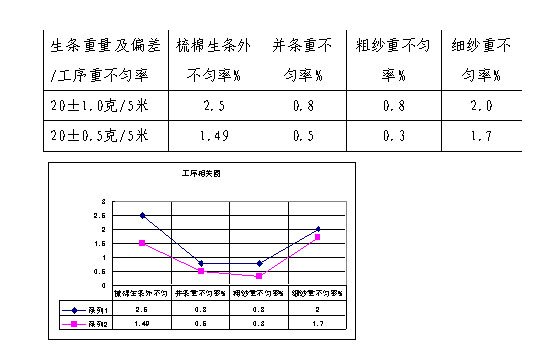
⑵梳棉机组各台梳棉机输出生条重量平均值的一致性显著影响生条外不匀率大小;即,系统的均匀控制装置对生条重量能否长时间保持生条重量的设定值,使之漂移最小,反映了系统均匀控制装置的可靠性和稳定性;
⑶工艺实验人员能否在调节定量过程中,把系统均匀控制精确地调节达到设定的生条重量值;应该指出:这与设定生条重量偏差调整范围及操作准确性直接有关;
⑷均匀喂棉装置调整准确性影响多机台生条重量值的一致性;
⑸梳棉机组各单机落棉率的差异,产量的差异,揩平车后各机台参数的重新设定等因素,都会影响机组重量外不匀率和重量偏差;
四、 结束语
通过系统分析清梳联工艺过程的工序质量的不断提高,可以充分说明青岛清梳联生产线在纺纱过程中取得优良质量品质的工艺设计思想:连续、均匀喂给;薄喂、柔和开松;分梳、梳理适度;气流参数保证;结、杂、短绒兼顾.的正确性和有效性.随着清梳联工艺技术的不断发展,科学实践的不断深化,对其认识还会不断地提高.实现从原料加工到成纱质量的不断优化;