1 配棉方案及工艺流程
根据后道工序对棉纱质量的要求进行科学配棉,配棉方案做到既确保棉纱质量,又降低生产成本。以T/C 65/35 58 tex 0E纱品种为例,配棉方案如下:等级4.7,品质长度29.77 mm,主体长度27.21 mm,细度1.52 dtex,强力2.83 CN,成熟度1.25,短绒率13.2%,含杂率3.6%。
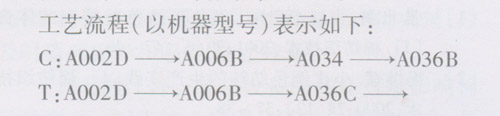
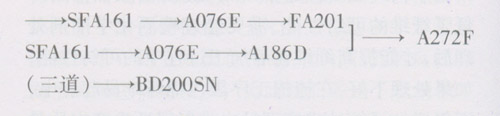
2各工序工艺要点
2.1 除尘系统
除尘系统是纺纱厂的环保工程,在纺纱生产中起到非常关键的作用,不但可以改善生产环境,减少空气污染,而且最重要的是有利于原棉中的尘杂的清除,达到提高产品质量的目的。转杯纺车间原先使用的是转笼式除尘设备,不仅能耗高,故障多,占地面积大,而且除尘效率比较低。为此,技术人员运用系统工程原理,对除尘系统进行重新设计,安装了目前国内最先进的JYF0一Ⅲ一8型蜂窝式除尘系统。该装置能耗低,维护简便,占地面积又小,过滤后的空气含尘量低于1 mg/m3,机台的工艺吸风畅通、稳定,杜绝了过去排杂风管堵塞的现象。
2.2清棉工序
在配棉等级较低的条件下,工艺设置以“多松少打,早落少碎”为原则,减少棉纤维的损伤,提高清棉除杂效率,降低棉卷重量不匀率。采取的具体措施如下。
(1)将A034型六辊筒开棉机中的一、三、五圆柱形打手和A036B型豪猪式开棉机的u型打手改为双刃刀片式打手,同时以自由打击为主,握持打击为辅,合理配置各打手的转速,这样既能减少棉纤维的损伤,又能提高棉块的开松度,提前分离棉杂,实现“多松少打,早落少碎”,提高了清棉工序的除杂效率。改造后的清棉除杂效率由45%上升至56%。
(2)将A092A型双棉箱给棉机改成SFA161型振荡棉箱,并合理配置输棉帘、角钉帘和打手的速度,合理设定角钉帘与均棉罗拉的隔距及棉箱的振荡频率。改进后,棉卷的横向均匀度提高且棉卷成形好,减少了梳棉棉网破边、破洞现象,提高棉花一次投入产出合格率。
(3)将各棉箱的水银开关全部改成光电开关,提高棉箱储棉量控制的灵敏度,保证各箱的储棉量合理流动,从而降低棉卷的纵向不匀率,提高棉卷正卷率。改造后棉卷的重量不匀率由1.5%下降到1.1%,棉卷的正卷率由93%上升到100%。
2.3梳棉工序
采用“紧隔距,中定量”工艺配置,并对梳棉机进行了以下改进。
(1)针对梳棉机预分梳板的针尖磨成圆角、锋利度下降且无法更换的情况,将预分梳板全部改成除尘刀和小漏底结构。在工艺配置上适当提高刺辊的转速,除尘刀采用低刀、大角度、紧隔距,小漏底采用短弦、进口大、出口小。改造后车肚落棉含杂率从原来的43%提高到57%。
(2)采用变频技术,将道夫传动方式由原电磁离合器传动改为直接电机变频传动,使道夫从低速到高速转动平稳,简化了传动机构,保证了棉网的质量,提高了生条均匀度。
2.4并条工序
牵伸配置采用顺牵伸,后牵伸头并大,二、三并小,熟条轻定量。对导条方式进行技术改造,将平台被动喂入方式改成高架积极喂入方式(配光电自停装置),减少棉条的意外牵伸,又避免缺条、粘条和涌条现象。改造后纺出的熟条弯钩纤维少,混纺比准确,棉条重量和条干均匀度好。
2.5转杯纺工序
工艺配置以输送纤维的气流流速合理地梯度增加为原则,进行纺杯、分梳辊和引纱速度的优选,并根据品种纤维配比变化选择合适的分梳辊针布型号。另外,对BD200SN型转杯纺纱机进行了系统化技术改造。
(1)采用变频技术,将车头的上、下两个齿形链条传动的变速箱分别改成电机变频同步齿形带传动,这样不仅传动平稳,降低了成纱重量变异系数和单强变异系数,而且简化了设备维修保养方法,省时省力省料,生产不同品种时工艺调整也方便、快捷、高效。
(2)对关键部件的维修和校正方式进行了技术改进,确保了纺杯、分梳辊、压辊的动平衡,缩小锭与锭之间的差异,降低棉纱的捻度不匀率,同时延长了专用配件的使用寿命。
3成纱质量
T/C 65/35 58 tex OE纱的物理指标见表1
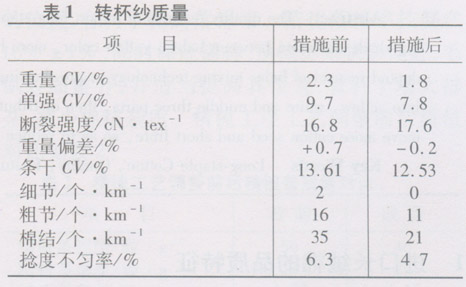
4 结束语
在转杯纺涤棉混纺起绒纱的生产中,在配棉等级较低的条件下,通过采用新工艺、新技术,不仅成纱质量有明显的改善,而且各道工序的回花量和疵纱大幅度减少,设备维修保养简便,机物料消耗降低,生产环境改善,生产成本降低,大大提高了企业的经济效益。