涡流纺纱技术是日本村田公司的专利技术,与以往的喷气纺纱技术的不同之处在于纱线结构接近与环锭纺相似的真捻,而且可以加工纯棉纱,纺纱强力与同支环锭纱相接近。影响涡流纺纯棉纱性质的因素有许多方面,但涡流纺的输出速度、喷嘴压力及纺纱支数等三因素都对涡流纱的性质有显著影响,涡流纱的性质有:条干不均率、纱疵、毛羽及单纱强力等。假如引出速度增加,纱线的毛羽增加、棉结减少。当喷嘴压力增加,纱的不匀率、粗节、棉结、强力都相应增加,但涡流纺纱线的毛羽会相应减少,一般情况下粗支涡流纱的物理性能毛羽及强力比细支纱好。
关键词:涡流纺、毛羽、条干均匀度、棉结、单纱强力、引出速度、喷嘴压力。
一、涡流纺纱(MVS)是一项比较有发展前途的新型纺纱技术:
村田公司生产的涡流纺纺纱机,可以加工纯棉纱,将喂入棉条拉细并加捻纺成涡流纱。当纤维从前罗拉引出后,立即被吸入喷嘴上的螺旋管中,接着纤维相互间靠紧并使束纤维向前运动到从螺旋喷嘴突出的针尖处,此时纤维受气流作用而加捻,加捻运动向上扩展。从螺旋喷嘴突出的针状物阻止捻度向上扩展,因此,上部针尖与前罗拉钳口之间的一些纤维被分离,但这些纤维在经过吸嘴后,仍然保持松散状,上部的纤维在旋转气流力的作用下开始膨胀,并经过固定的空心锭子,涡流围绕着纤维束芯,并使纤维束成功的形成MVS纱,在受到检验并去除疵点后即卷绕成筒子纱。
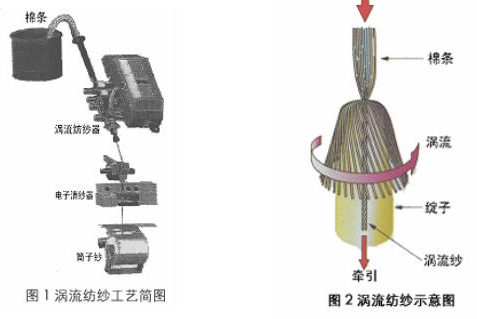
涡流纱是由平行纤维组成的纱芯,并由许多包缠纤维缠绕在一起形成。分析纱线的结构,涡流纱与一般喷气纱十分不同,包缠纤维占的比例较多,包缠纤维及平行纱纤维两部分组成的纱线结构,涡流纺从束纤维外转分离出形成的数量大的包缠纤维,比喷气纺的外转包缠纤维的数量多的多。
对喷气纺与涡流纺性质区别的研究,应用不同的比例的涤棉纱,发现涡流纱的条干比喷气纱好的多,相比之下粗节疵点少,毛羽少。100%涡流纺还具有比喷气纺有较高的强力及极低的伸率。
涡流纱的基本性质与引出速度、喷嘴压力及纺纱支数等有关,现对MVS851涡流纺纱机生产涡流纱进行一些对比试验及讨论。
二、试验:
为了说明涡流纺的喷嘴压力、引出速度及纺纱支数对涡流纱性质的影响,国外一研究机构选用了27种不同类型的棉纤维普梳纱样,都是由MVS851涡流纺生产的:
试验原棉具有如下性质
马克隆值气流读数值4.45,纺纱长度29.89毫米,长度不匀率2.5%,断裂强力28.81克/tex,右半部平均长度28.37,长度不匀率46.6%,不匀率指数826断裂伸长率5.2%。
对于性能良好的MVS851的纺纱效率及纺质量纱,要想都达到理想水平,尤其要注意供应的棉条准备。应用三道并条机加工熟条喂入涡流纺纱机,主要为了改善纤维的排列及喂入棉条的均匀度,试验用RSB 851二道及一道RSB D-35,在经过三道并条后,熟条的线性密度为2.48ktex,试验方案结果如下:
表1 试验编组
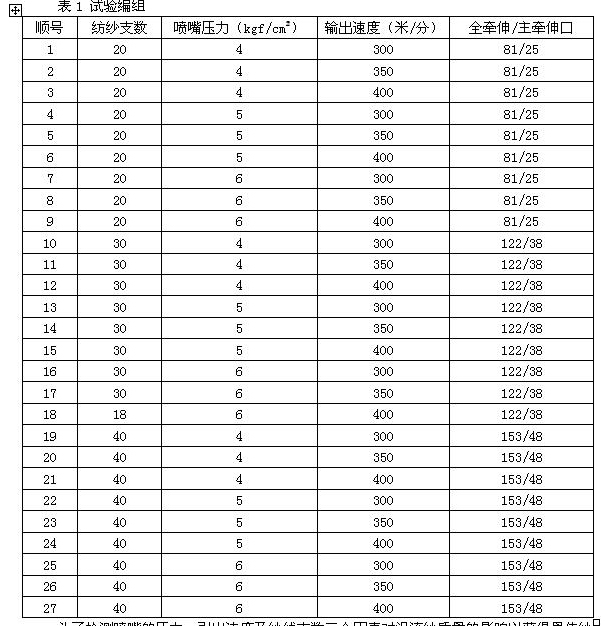
为了检测喷嘴的压力,引出速度及纱线支数三个因素对涡流纱质量的影响以获得最佳纱线特性,共设有三种喷嘴压力,分别是4、5、6kgf/cm2,三种输出速度,300、350、400米/分,及选取三种不同的纱支20S、30S及40S,所有的纱在如下条件下生产,70°喷气发射角、2P130dL7-9.3型针孔、1.2毫米锭子内直径、36-36-49毫米上罗拉隔距及36-36-44.5下罗拉隔距涡流纺纱机为MVS851型。
将上述取的纱样进行对比,主要对比纱线不匀率、纱疵、毛羽、强力、伸长率及断裂功值,纱线在Uster Tester4 SX及在Tensorapid试验断裂强力及断裂伸率及B-Work,纱线毛羽试验是应用Zweigle G565毛羽试验仪,将试验结果进行分析其不同之处,应用三种方法反复试验分析变化情况。
三、试验结果及讨论:
1、纱线不匀率及纱疵特性:
表2所示为涡流纱线以不同的喷嘴压力,不同输出速度,生产不同的纱支的不匀率及纱疵的试验结果,表明纱线的引出速度及纱支对纱线不匀率及纱疵影响显著。
表2 涡流纺、喷嘴压力、引出速度及纺纱支数对纱线不匀率、纱疵性质的影响对比分析表:
表2
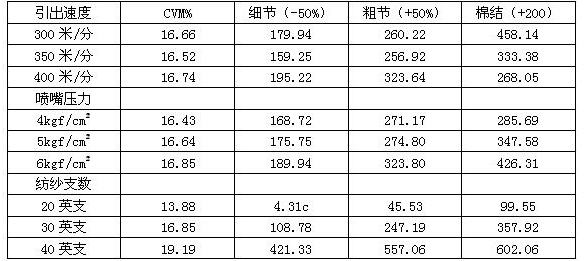
表3 纱线不匀率对比(喷嘴压力4、5及6kgf/cm2,引出速度300、350及400米/分)
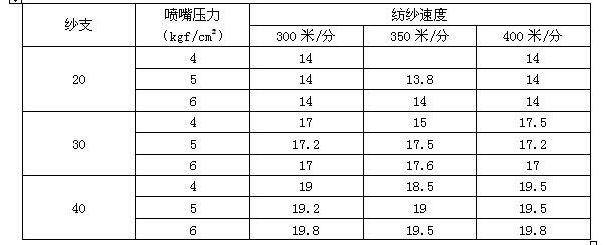
表3所示,不同喷嘴压力4、5、6 kgf/cm2及不同的引出速度300、350、400米/分,不同纺纱支数20英支、30英支及40英支的条干不匀率的对比,从表2中可看出纱线条干及粗节的变化情况,可以看出在较高的引出速度时,喷气流的效率减少,而且棉结在引出速度增加时相应减少,有三个最佳点在引出速度300、400米/分之间纱线条干及纱疵优于其它。
细支纱统计值比粗支纱具有较高的条干不匀率及较多的细节、粗节及棉结,见表2
经对喷嘴压力的分析,喷嘴压力对于涡流纱的细节、粗节及棉结的影响并不明显,涡流沙的不匀率、棉结、粗、细节值,在低喷气压力下,比高气压时好,喷嘴压力从5至6kfg/cm2增加时,显著影响涡流纱的粗节值,而且喷嘴压力在4-5kgf/cm2压力的增加95%不产生任何影响,较高的喷嘴压力可以增加纤维的损失量,从而增加了涡流纱的不匀率。
2、纱线毛羽性质:
将MVS涡流纱在乌斯特试验仪4SX及Zweigle G566毛羽测试仪上试验,测试出毛羽值,1毫米、2毫米及S3代表全部毛羽数值,从3毫米上升到25毫米,从纱的表面及乌斯特毛羽指数(表4)为纱线毛羽的测试结果,分别以乌斯特毛羽指数及S3表示,按照试验结果,引出速度、喷嘴压力及纱线支数都显著的对涡流纱的毛羽有显著影响,表5所示,当引出速度增加,毛羽值(S3-Zweigle)相应增加,表4所示,纱线的毛羽指数(乌斯特)在不同的喷气压力及不同的引出速度条件的对比。
表4
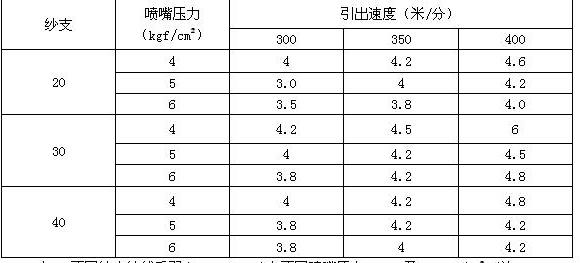
表5 不同纱支纱线毛羽(S3-Zweigle)在不同喷嘴压力4、5及6 kgf/cm2,以300、350及400米/分引出速度条的对比
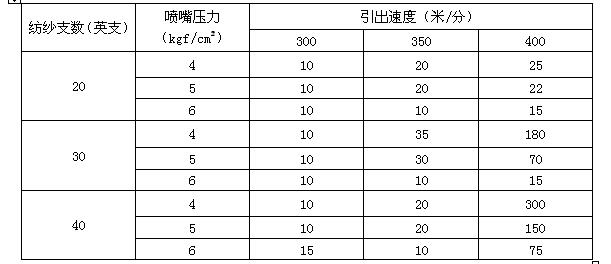
表6 引出速度、喷嘴压力及纱线支数对涡流纱毛羽性质的影响(喷嘴压力4、5及6 kg/cm2,引出速度300、350及400米/分)
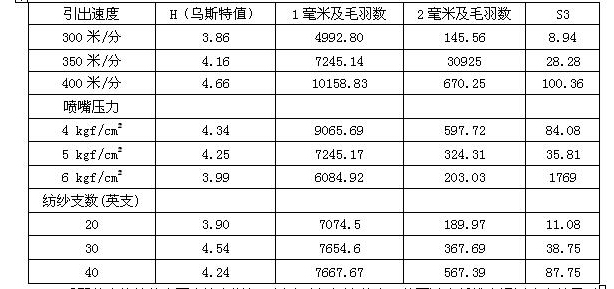
毛羽值高使纱的表面摩擦力增加,减少喷气气流效率,从而减少纤维在通过空心锭子时的旋转。
相反,在输出速度作用下,纱线的毛羽因喷嘴的压力增加而减少,在高压喷嘴压力下,毛羽相应减少,这可认为是喷嘴气流压力增加喷嘴气流的螺旋力因压力增加受到影响,毛羽值上升形成较好的包缠效果。
按照纺纱支数,毛羽值、2毫米及S3在纺细支纱时增加,但在乌斯特毛羽1毫米级时并不明显。
3、纱线的强力性质:
表7、表8所示为涡流纱的强度及伸率变化,不同的纱支及喷嘴压力4、5及6 kg/cm2,引出速度300、350及400米/分,断裂强力及伸长率B-断裂功显著的受到引出速度、喷嘴压力及纱线支数变化的影响,所有的强力数值因引出速度增加而减少,但喷嘴压力增加会使强力及伸率值增加(表8)有较高的强力值。
表7,喷嘴压力值4、5及6 kgf/cm2,引出速度300、350及400米/分的涡流纱20、30及40英支纱的强度比较
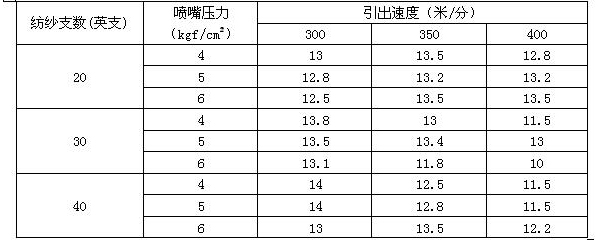
表8 涡流纱的断裂伸长率比较

20英支、30英支及40英支,喷嘴压力4、5及6 kgf/cm2,引出速度300、350及400米/分
所有试验值表明,因引出速度增加而断裂伸长值减少,但当喷嘴压力增加(表9),喷嘴压力6 kg/cm2比4、5 kgf/cm2压力涡流纱的强力增加,此时涡流纱包缠的好,包的紧,而且包缠的长。
按照反复试验结果,纺纱支数也很显著的影响涡流纱的强力及伸率及断裂功,这些涡流纱的性质因纱支变细而降低,但涡流纱的强力、伸率基本不受喷嘴压力及纱支的干扰。
表9
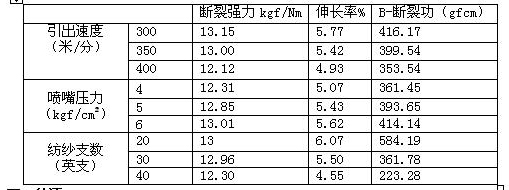
四、结语:
涡流纱的性质显著的受引出速度、喷嘴压力及纺纱支数的影响,涡流纱的棉结数因引出速度增加而减少,涡流纱的强度因生产速度增加而降低,纱线毛羽因引出速度增加而增加。
喷嘴压力对涡流纱性质的影响很显著,减少喷嘴压力可改进涡流纱的均匀度及纱疵(细节疵点除外),喷嘴压力对涡流纱的细节影响显著,因此,可认为增加喷嘴压力,由于使涡流纱包缠的好,可显著的改进纱线毛羽及强力性质。纱线支数与纱线性质十分相关,一般粗支纱的性质、条干均匀度、纱疵、毛羽及强力性质等。
合理的选择引出速度、喷嘴压力及纺纱支数都会显著改进涡流纱的性质,可以使涡流纱达到最佳的特性,换言之,可像环境纱及转杯纱纺纱技术那样,涡流纱可以获得最佳的最终产品的用途。